Negative Pressure Isolators
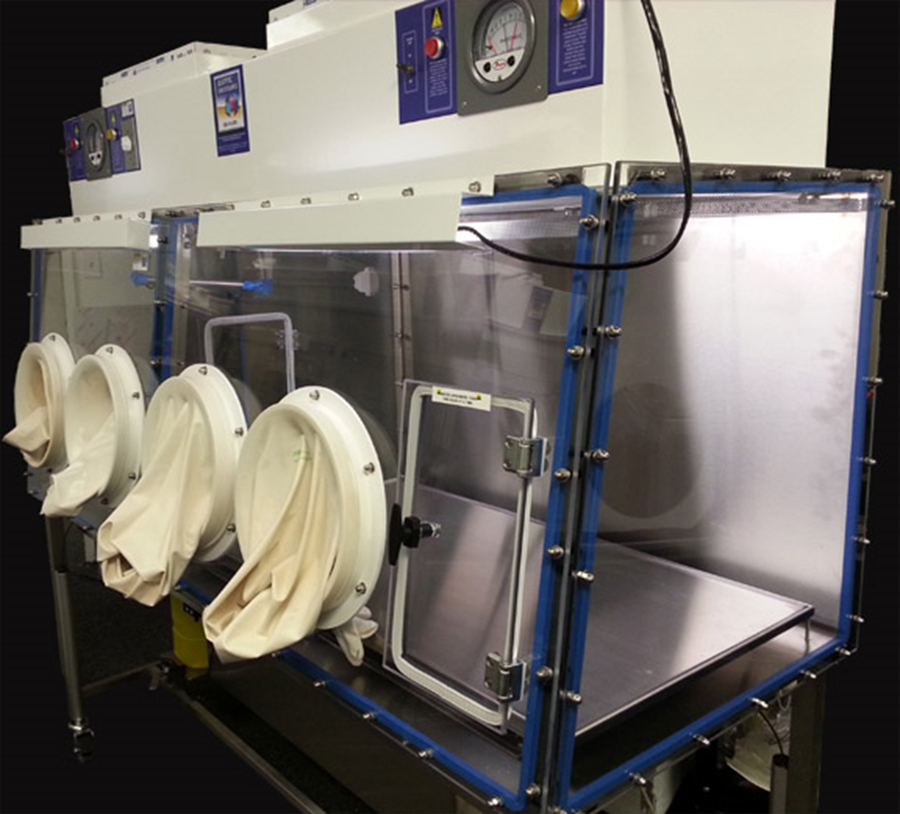
Superior Protection Through Advanced Containment Technology
Negative pressure isolators represent the gold standard in hazardous drug compounding safety. Unlike traditional Biological Safety Cabinets (BSCs), our containment isolators provide unmatched protection for both pharmacists and the surrounding environment while maintaining perfect aseptic conditions.
Complete USP-800 Compliance in One System
Our negative pressure isolator systems uniquely combine:
- Containment Segregated Compounding Area (C-SCA) functionality
- Containment Primary Engineering Control (C-PEC) requirements
- Compounding Aseptic Containment Isolator (CACI) specifications
This comprehensive approach eliminates the need for separate containment systems, saving valuable pharmacy space while enhancing safety protocols.
XLTC 800: The Ultimate Negative Pressure Isolator Chamber
The XLTC 800 represents our flagship containment isolator system, featuring:
- Multi-Chamber Design: Includes negative pressure staging chamber, processing chamber, and direct compounding area
- Enhanced Protection: Materials transfer through progressive pressure zones
- Complete Isolation: Handling occurs exclusively through gloves and sleeves
- Unidirectional Airflow: Maintains particulate-free environment throughout the isolator chamber
- Integrated Storage: Optional refrigeration for temperature-sensitive medications
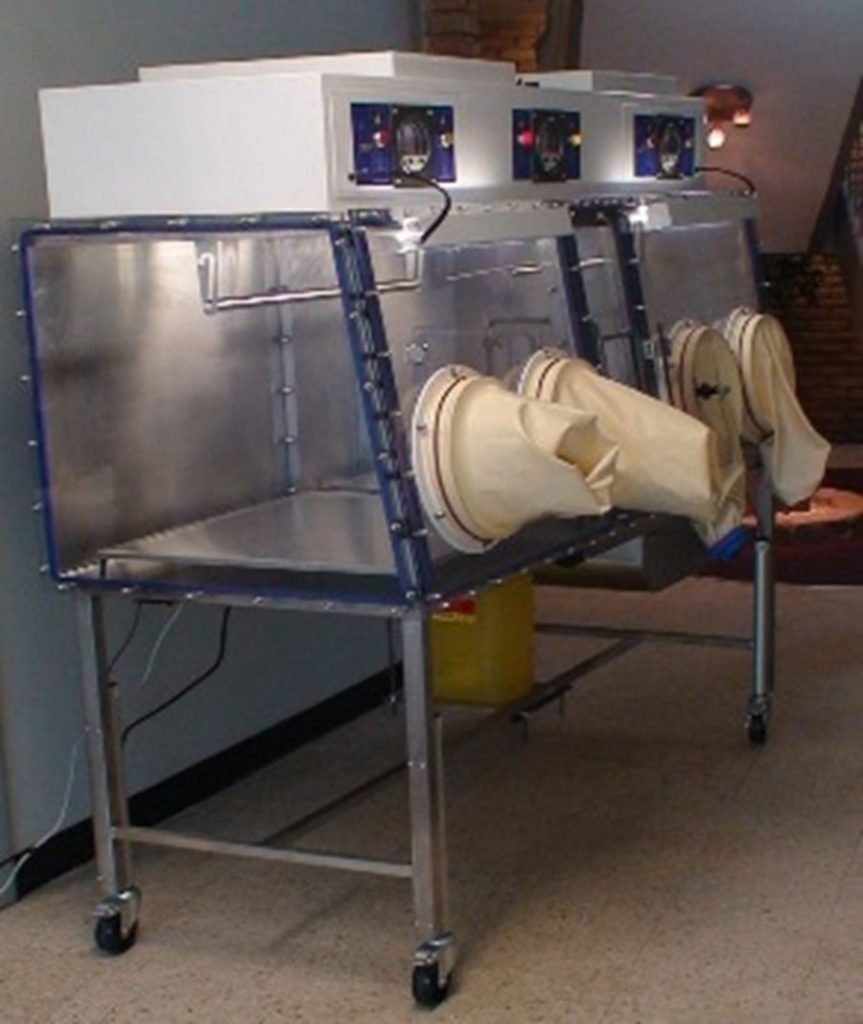
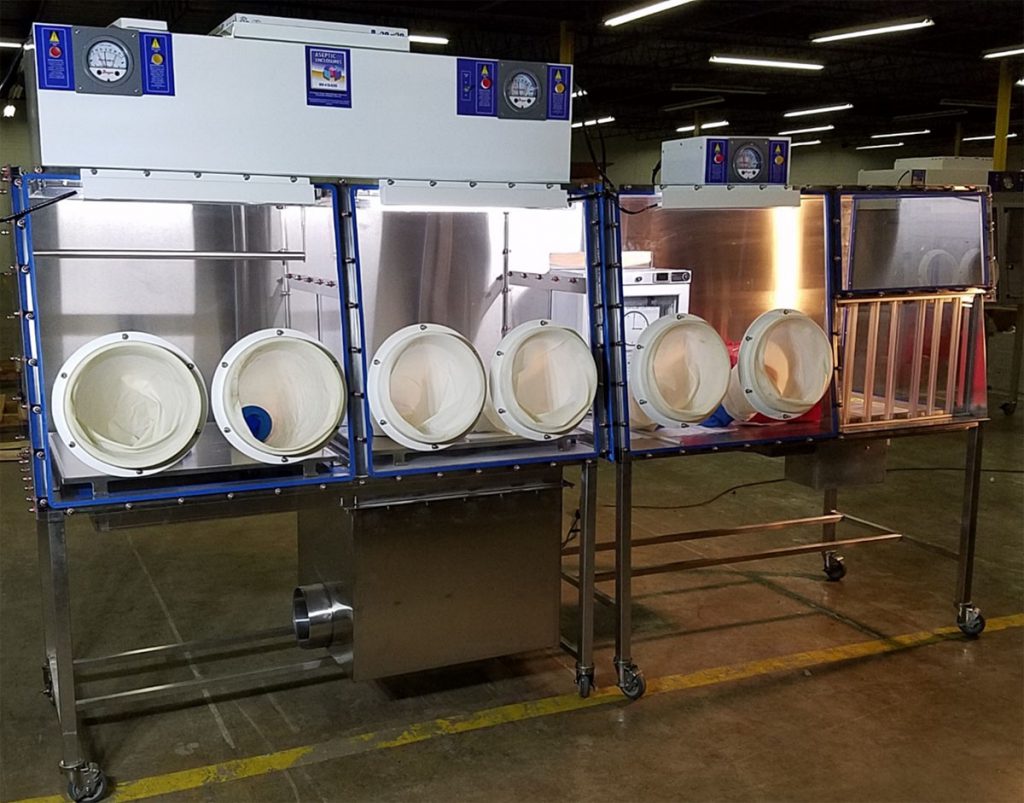
Regulatory Compliance Guaranteed
Every negative pressure isolator we manufacture is certified to meet or exceed:
- USP <797> Sterile Compounding Standards
- USP <800> Hazardous Drug Handling Requirements
- NIOSH Guidelines for Hazardous Drug Safety
- CETA Certification Standards
- FDA Aseptic Processing Guidelines
Advanced Safety Features
Our pressure isolators include critical safety enhancements:
- Comprehensive containment alarm system requiring manual acknowledgment
- Continuous negative pressure monitoring
- HEPA filtration for both intake and exhaust
- Documented leak rate <0.05% for maximum containment
Applications for Negative Isolators
AsepticEnclosures negative pressure containment isolators are ideal for:
- Hazardous Drug Compounding: Superior protection for chemotherapy preparations
- Nuclear Pharmacy Operations: Safe handling of radioactive materials
- Specialty Pharmacy Applications: Custom containment isolator configurations
- Research Facilities: Controlled environments for sensitive materials
Customization Options
Our aseptic containment isolator systems can be tailored with:
- Automated picking chambers for robotics integration
- Extended staging areas for improved workflow
- Pass-through chambers for efficient material transfer
- Custom dimensions to fit existing infrastructure