Design Build Isolators
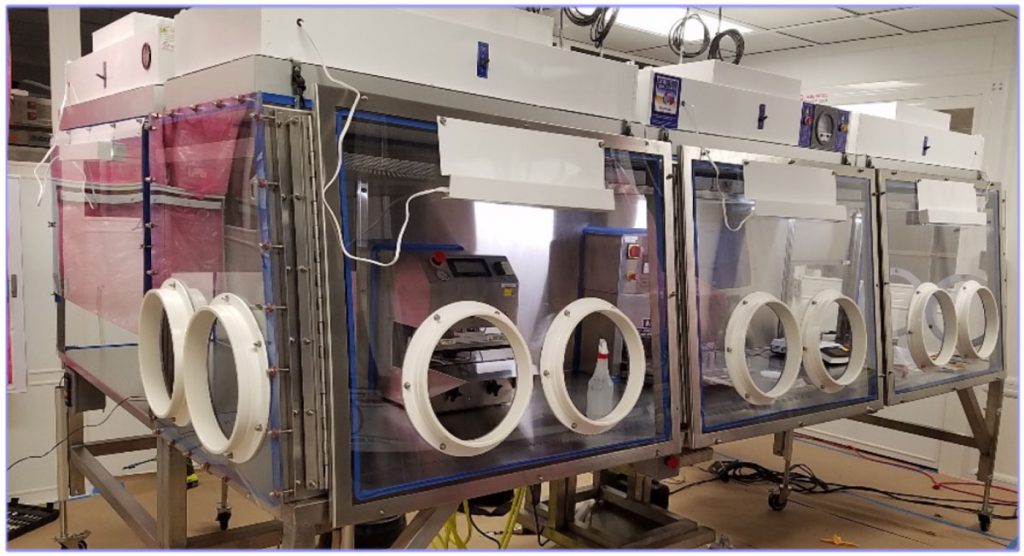
Custom Isolator Solutions for Critical Applications
AsepticEnclosures specializes in advanced isolator design and manufacturing for pharmaceutical, healthcare, and research applications. Our custom isolator systems provide optimal contamination control with efficient project implementation.
Comprehensive Isolator Design Solutions
Our design build process delivers:
- Expert process evaluation and needs assessment
- Custom isolator design tailored to your application
- Efficient production with rigorous quality control
- Rapid approval-to-installation timeframe (typically 8 weeks)
- Significant cost savings compared to competitors
Applications for Our Isolators
We provide specialized solutions across multiple industries:
- Pharmaceutical isolators for sterile manufacturing
- Aseptic isolators for critical processing
- Pharmacy isolators for USP compliance
- Research containment systems
- Healthcare isolation environments
- Custom applications for unique processes
The AsepticEnclosures Advantage
Our isolators for pharmaceutical applications combine:
- Innovative design approaches
- Superior containment performance
- Enhanced ergonomics for operator comfort
- Optimized workflow configurations
- Validated cleaning and decontamination processes
Contact our team to discuss how our custom isolator solutions can enhance your operations while reducing implementation time and costs.
Many modules and custom designs available.
Contact us today!
Frequently Asked Questions
What are custom isolators and how do they differ from standard isolators?
Custom isolators are specialized containment units designed to meet specific user requirements, offering greater flexibility and customization options compared to standard isolators. They are tailored to the specific processes and needs of a particular application, providing enhanced performance and safety.
What industries benefit most from the use of custom isolators?
Industries such as pharmaceuticals, biotechnology, healthcare, and electronics benefit most from custom isolators. These isolators provide a controlled environment for sensitive processes, ensuring safety, contamination control, and compliance with regulatory standards.
What are the key features to consider when designing a custom isolator?
Key features to consider include the isolator's size and configuration, materials of construction, filtration systems, airflow patterns, pressure controls, ease of cleaning, ergonomic design, and compliance with industry standards and regulations.
How can custom isolators improve safety and contamination control in a lab?
Custom isolators improve safety and contamination control by providing a sealed environment that prevents the escape of hazardous materials and contaminants. They are designed to meet specific requirements for airflow, filtration, and pressure differentials, ensuring that the working environment remains safe and free from contamination.
What materials are typically used in the construction of custom isolators?
Materials commonly used in custom isolators include stainless steel, glass, acrylic, and other durable, non-reactive materials. These materials are chosen for their ability to withstand decontamination processes, resist corrosion, and maintain structural integrity under various operating conditions.
How are custom isolators validated for their intended use?
Custom isolators are validated through a series of tests and qualifications, including installation qualification (IQ), operational qualification (OQ), and performance qualification (PQ). These tests ensure that the isolator meets design specifications, operates correctly under standard conditions, and performs reliably in actual use scenarios.
What are the common applications of custom isolators in the pharmaceutical industry?
In the pharmaceutical industry, custom isolators are used for applications such as sterile compounding, aseptic processing, containment of potent compounds, quality control testing, and research and development. They provide a controlled environment to prevent contamination and ensure product integrity.
How can custom isolators be integrated into existing laboratory setups?
Custom isolators can be integrated into existing laboratory setups by assessing the current lab layout, identifying space and utility requirements, and designing the isolator to fit seamlessly within the available space. Proper planning and coordination with lab personnel and facility managers are essential for a smooth integration process.
What are the maintenance requirements for custom isolators?
Maintenance requirements for custom isolators include regular cleaning and decontamination, routine inspection and replacement of filters, calibration of sensors and control systems, and timely repair of any damaged components. Adhering to a comprehensive maintenance schedule ensures the isolators remain effective and reliable over time.