How to meet USP 800 standard
XLTC800 exceeds the minimum standards established by USP800
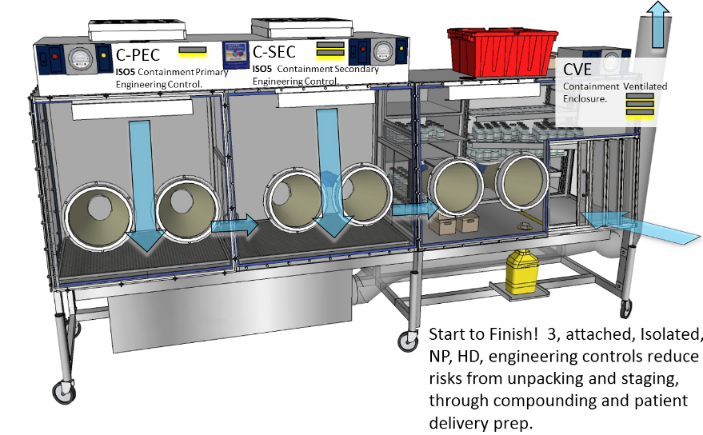
Which areas do you feel have more exposure risk?
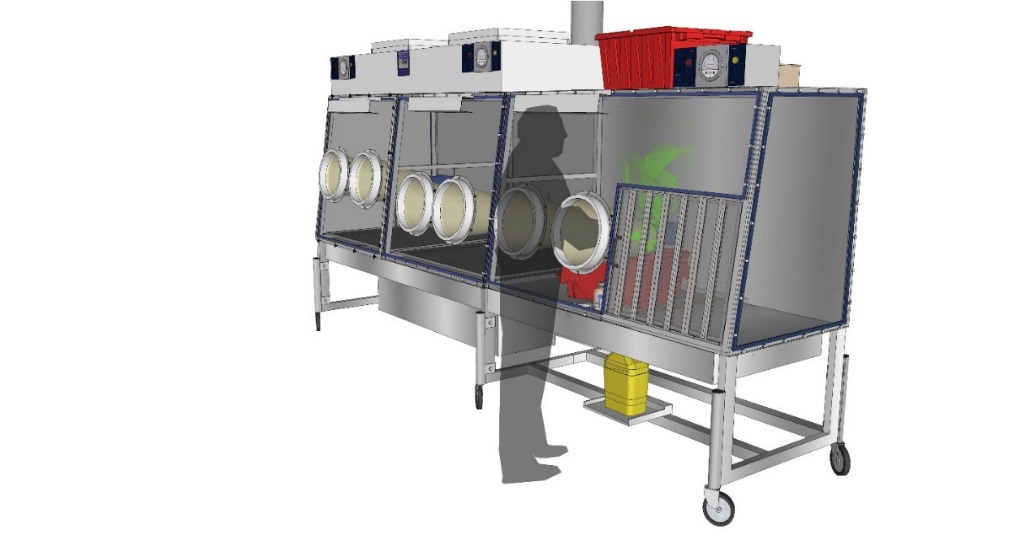
XLTC800
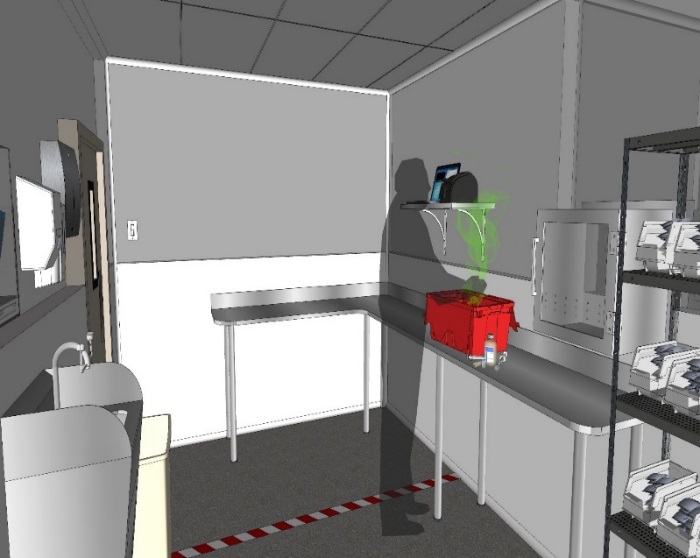
Negative Pressure HD Staging Room
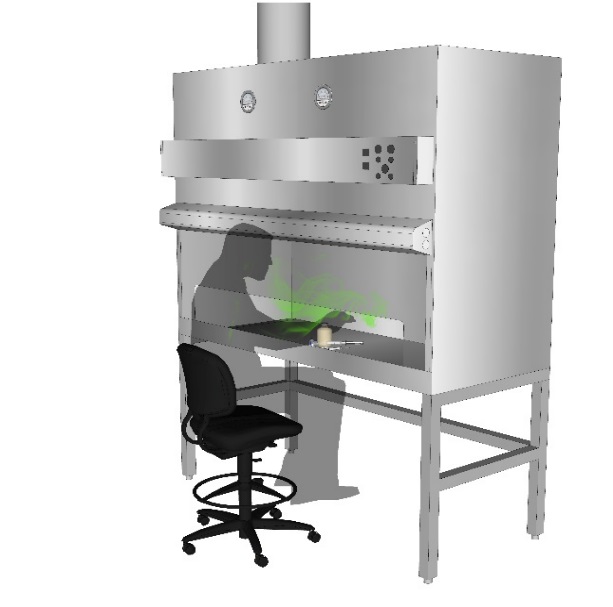
Biological Safety Cabinet
How to meet USP 800 Standard
In the below table the left column is extracted directly from USP800, the right is our comparison and comments.
USP800 | XLTC800 |
5. FACILITIES AND ENGINEERING CONTROLS HDs must be handled under conditions that promote patient safety, worker safety, and environmental protection. Signs designating the hazard must be prominently displayed before the entrance to the HD handling areas. Access to areas where HDs are handled must be restricted to authorized personnel to protect persons not involved in HD handling. HD handling areas must be located away from breakrooms and refreshment areas for personnel, patients, or visitors to reduce risk of exposure. Designated areas must be available for: • Receipt and unpacking • Storage of HDs • Nonsterile HD compounding (if performed by the entity) • Sterile HD compounding (if performed by the entity) Certain areas are required to have negative pressure from surrounding areas to contain HDs and minimize risk of exposure.
| The XLTC 800, by design, restricts ALL personnel from ALL HD handling areas.
|
5.3.2 STERILE COMPOUNDING In addition to this chapter, sterile compounding must follow standards in <797>. All C-PECs used for manipulation of sterile HDs must be externally vented. Sterile HD compounding must be performed in a C-PEC that provides an ISO Class 5 or better air quality, such as a Class II or III BSC or CACI. Class II BSC types A2, B1, or B2 are acceptable. For most known HDs, type A2 cabinets offer a simple and reliable integration with the ventilation and pressurization requirements of the C-SEC. Class II type B2 BSCs are typically reserved for use with volatile components. Appendix 3 describes the different types of BSCs.
| XLTC800: C-PEC, C-SEC and CVE are externally vented through HEPA exhaust filters. The C-PEC and C-SEC run far better that ISO Class 5, at all times. |
The C-PEC must be located in a C-SEC, which may either be an ISO Class 7 buffer room with an ISO Class 7 ante-room (preferred) or an unclassified containment segregated compounding area (C-SCA). If the C-PEC is placed in a C-SCA, the beyond use date (BUD) of all compounded sterile preparations (CSPs) prepared must be limited as described in <797> for CSPs prepared in a segregated compounding area. Table 3 summarizes the engineering controls required for sterile HD compounding.
| Our C-PEC is ISO Class 5. In fact, it runs at 0 particulate levels at virtually all times regardless of surrounding activities. It can only be opened to the adjacent C-SEC which also runs ISO class 5. Our C-SEC runs negative to the C-PEC. Aseptically, a far superior approach to having a positive pressure Ante dump into a negative pressure buffer. The attachment of a CVE (for opening shipments) that is Negative to C-SEC adds another level of Aseptic protection against particulate ingress (See above model for airflow and pressure representations) |
ISO Class 7 buffer room with an ISO class 7 ante-room: The C-PEC is placed in an ISO Class 7 buffer room that has fixed walls, HEPA-filtered supply air, a negative pressure between 0.01 and 0.03 inches of water column relative to all adjacent areas and a minimum of 30 ACPH.
| Again, due to our ability to run the C-PEC Negative, but positive to the C-SEC particulate ingress is only possible if it rides in on poorly wiped containers. |
The buffer room must be externally vented. Because the room through which entry into the HD buffer room (e.g., anteroom or non-HD buffer room) plays an important role in terms of total contamination control, the following is required:
| All areas of the XLTC800 are externally vented. Additionally, it eliminates contamination risks associated with moving HD’s through positive pressure, non-HD areas and the risks associated with unpacking and prepping those HD’s for cleanroom entry. |
• Minimum of 30 ACPH of HEPA-filtered supply air | The XLTC entry area, again runs negative to the C-PEC at approximately 1,000 ACPH for far greater particulate reduction potential. |
• Maintain a positive pressure of at least 0.02 inches of water column relative to all adjacent unclassified areas.
| Having to maintain a positive pressure entry zone greatly increases contamination risk. Countless studies prove this. |
• Maintain an air quality of ISO Class 7 or better. | ISO5, typically 0 ppsqft. |
An ISO Class 7 ante-room with fixed walls is necessary to provide inward air migration of equal cleanliness classified air into the negative pressure buffer room to contain any airborne HD. A hand-washing sink must be placed in the ante-room at least 1 meter from the entrance to the HD buffer room to avoid contamination migration into the negative pressure HD buffer room.
| The XLTC800 does not need to allow air to migrate in.
One most significant CFU risk factors in a cleanroom is the sink. (It should be nowhere near the entry to a buffer room!) The XLTC800 does not require a sink. |
Although not a recommended facility design, if the negative-pressure HD buffer room is entered though the positive-pressure non-HD buffer room, the following is also required:
| This design, really should not be allowed. HD containment is important in areas other than the buffer room. |
• A line of demarcation must be defined within the negative-pressure buffer room for donning and doffing PPE. | Of course, donning and doffing in a buffer room creates Hazardous waste and generates particulate, and not needed with the XLTC800. |
• A method to transport HDs, HD CSPs, and HD waste into and out of the negative pressure buffer room to minimize the spread of HD contamination. This may be accomplished by use of a pass-through chamber between the negative-pressure buffer area and adjacent space. The pass-through chamber must be included in the facility’s certification to ensure that particles are not compromising the air quality of the negative-pressure buffer room. A refrigerator pass-through must not be used. Other methods of containment (such as sealed containers) may be used. HD CSPs prepared in an ISO Class 7 buffer room with an ISO Class 7 ante-room may use the BUDs described in á797ñ, based on the categories of CSP, sterility testing, and storage temperature. | In the XLTC800 from the time the HD totes from your supplier are opened, until the HD preparations are ready for patient delivery, Hospital staff is protected by a comprehensive barrier that is under constant negative pressure.
Staff ARE NOT walking into a HAZARDUOUS Drug room!
Refrigerated storage as show in the above illustration is part of the negative pressure in the CVE. Most refrigerators are absolutely NOT cleanroom compatible. |
7. PERSONAL PROTECTIVE EQUIPMENT 7.2 When gowns are required, they must be disposable and shown to resist permeability by HDs. | PPE, is built into the XLTC800. Our PPE is ASTM6978-05 tested. Most traditional garbing is not. |
7.4 Eye and Face Protection | Always on. Built into our equipment. |
7.5 Respiratory Protection | Always on. Built into our equipment. No special training required. |
7.6 Disposal of Used Personal Protective Equipment | Because our PPE is built in, there is significantly less disposal required. Reducing exposure and aseptic risk. |
15. DEACTIVATING, DECONTAMINATING, CLEANING, AND DISINFECTING
| XLTC simplified design facilitates safer, and more effective cleaning, decontaminating and disinfecting and all of this can be done without personnel be exposed to the HD’s and significantly reduces issues with hazardous waste handling. |
17. DOCUMENTATION AND STANDARD OPERATING PROCEDURES
| Environmental monitoring of the XLTC800 is not just wipe sampling. The equipment enables real-time environmental monitoring and alarms if there is no negative pressure according to the requirements. |
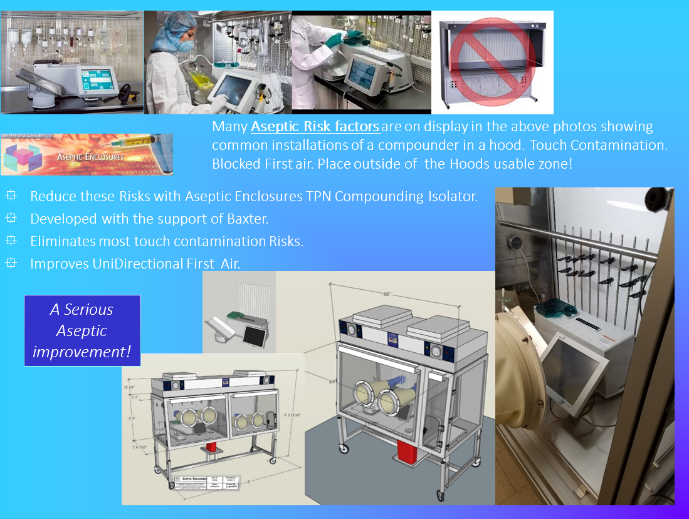
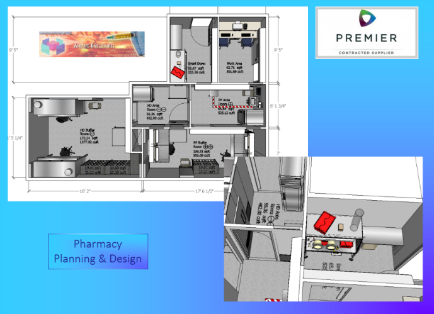